
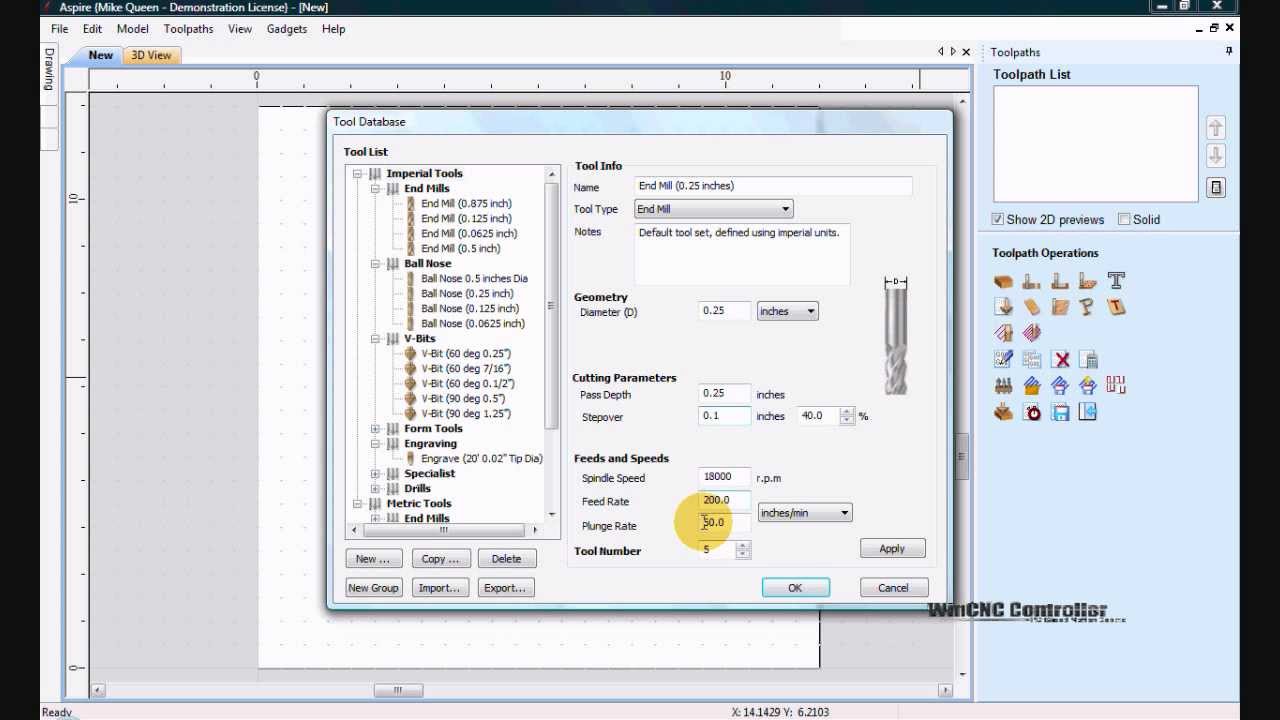
The hard part with these textures is the finish pass is always painful and you have to do the math on post processing cleanup vs machine run time. The end result will likley not be a machine issue but rather a finished product issue (bad finish). Your machine can likely withstand 10X what your throwing at it. Your either going to borderline stall your spindle (likely never happen) or break a tool (again likely never happen). I am hesitant to push my machine too hard without knowing the consequences.In my opinion in an operation like this there really arent any devastating consequences. I am hesitant to push my machine too hard without knowing the consequences. The answer with these to me is to rip off the roughing wide open as fast as your machine will run with the biggest tool possible leaving only what you absolutely need then get to your painfully slow finish pass. You can fudge both of these in a program like VCarve Pro or you can do it with Aspire/Fusion and rest machining. Second scenario would be two roughing passes with a large tool firs and the second tool only doing the final deep cleanup it can reach. Then hopefully you can have a single finish pass that will leave you with acceptable result. I would personally ditch the two roughing passes for a single roughing pass using the largest ball nose cutter you can run that will get into the detail and run as fast as possible ignoring your surface finish. Its a balance you you have to find that speaks to material, tool and machine rigidity, speed, and depth of cut. Killing or reducing the roughing passes is going to do to two things, increase your number of finish passes, and depending on final finish pass reduce your final surface quality.

Cheers, bobįirst off, your first/last image is pretty sweet.
#Vectric vcarve pro stepover full
However, I am assuming these bits are capable of cutting full height, but is it advisable for 9 hours? Any advice would be appreciated. I'm guessing the concern would be stress on the bit. Given the small stepover, is it possible to avoid the roughing passes and go directly to the finishing pass? Would save a couple of hours and bit changeover. The final finish was beautiful with only a couple of places with some torn grain that needed sanding (320 grit). The finishing pass was with a 5% step over. First with a 1/2" end mill (30 min) and a second with a 1/4 ballnose (1-1/2 hrs).įinally I did the finishing pass with an 1/8" tapered ballnose with a 1" cutting height (9 hrs). Abstract artsy-fartsy piece.Īs you can see there are some rather deep cuts (up to.

Hi, I purchased a CAMaster Stinger 1 2x4 (1.7kw spindle) a couple months ago and just completed my first 3D project (10"x10") in walnut shown below.
